
Our customers
Delve into our customer references to gain insights from real-life experiences of our partners.

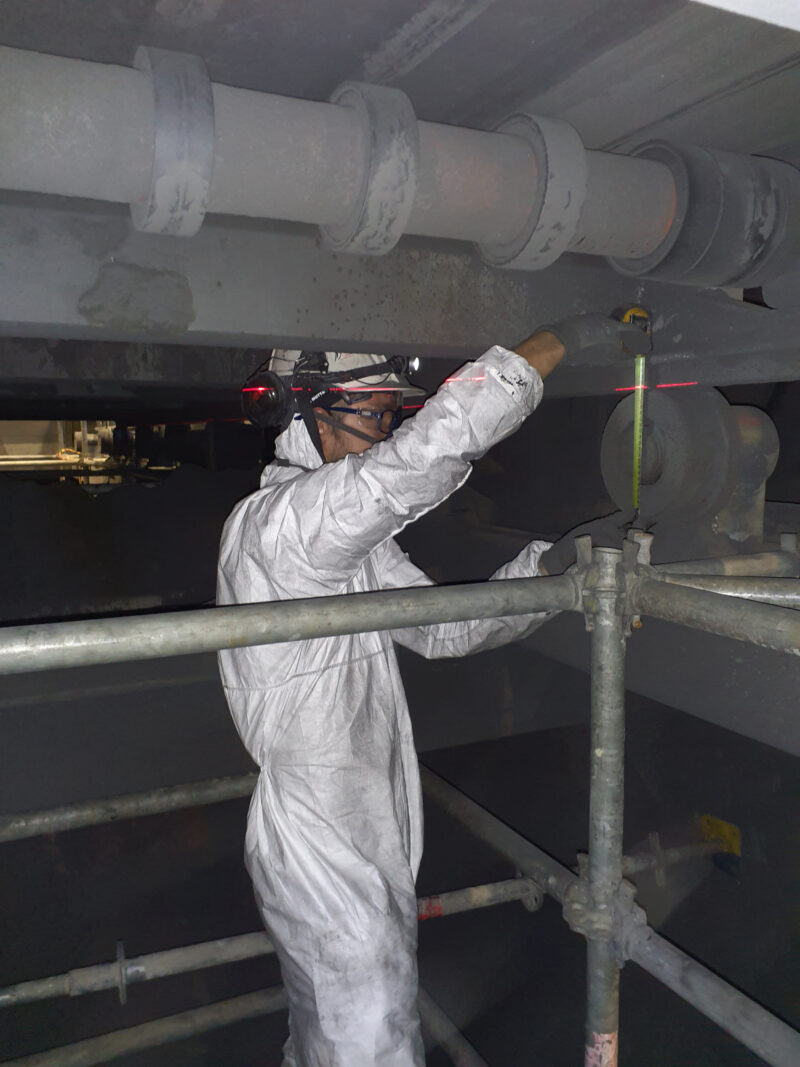
Going Above and Beyond in Conveyor Maintenance Services
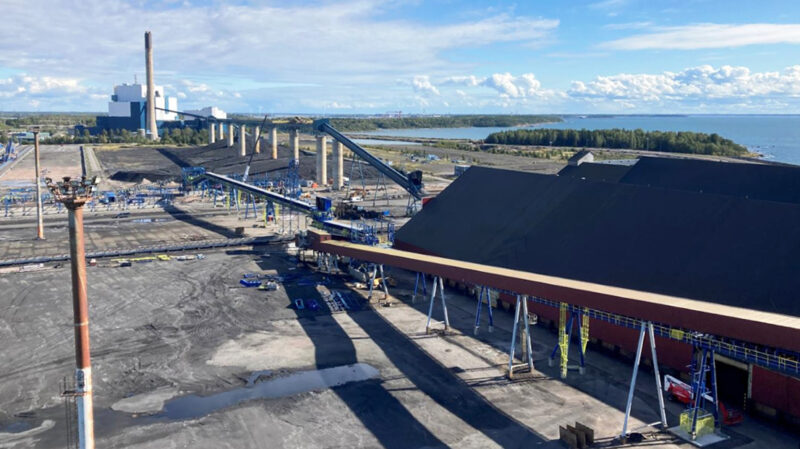
Delve into our customer references to gain insights from real-life experiences of our partners.