Disaster Avoided with the Help of ROXON HX270 Belt Condition Monitoring
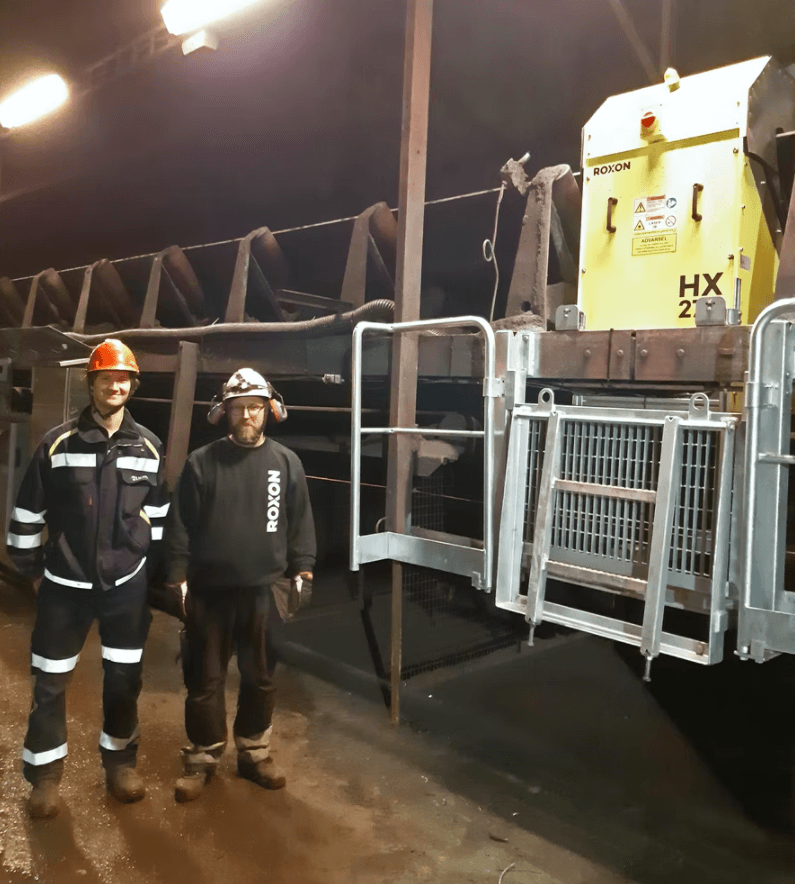
A major Scandinavian mining company decided to invest in HX270 for a second time after being satisfied by its performance since its initial installation in 2015. The second investment included 5 belt monitoring modules for two critical conveyors and was completed in 2019.
The new conveyors are approximately 630 m long with a capacity of 9000 t/h. The steel cord belts belts are roughly 1.3 km long and 2000 mm wide. Most of the material in the process is transferred trough these two conveyors, hence their importance to the customer.
HX270 is the most advanced conveyor belt condition monitoring control system in the world. The system includes fully automatic optical 3D belt surface scanning devices for both sides of the belt and a conveyor belt control feature. This enables the belt operator to drive the selected damaged part of the belt to a predefined location along the conveyor with full speed. The scanning devices are in the most crucial locations of the conveyor, immediately after the loading and unloading points, giving the most optimal reaction time for all belt damages. This makes it the most powerful tool for proactive maintenance of the conveyor belts.
HX270 detects all type of belt damages in textile and steel cord belts including belt rips, cuts, tears, holes, splice damages, steel cord damages, etc. This is possible because all the conveyor belt damages are visible on the surface of the belt. HX270 can replace all other condition monitoring devices in conveyor belt monitoring applications.
The customer transfers roughly about 17 Mt of material per year through these two conveyors. The net sales value of the production is several millions of Euros per day. HX270 was installed in August 2019 and the system proved its ultimate efficiency. During the night of February the 2nd 2020, a metal plate got stuck into the loading chute of the conveyor and started to damage the belt. HX270 stopped the belt before the total belt rip and the potential disaster was avoided.
The loss would have been tremendous if the entire conveyor belt had been ripped. The customer was able to do a planned repair for the damages and production continued. The potential disaster was due to the earlier conveyor belt rip.
Prior to investing in HX270, the lead time for a spare conveyor belt was several months. If the customer would have lost the conveyor belt, it would have had major impact on the entire production of the company. The potential production loss would have been enormous in addition to repair costs.
It is clear that the investment can be considered paid back already and that HX270 is now a critical piece of equipment for their operation.
Click here to find out more about HX270, or contact us to speak to a technical specialist.